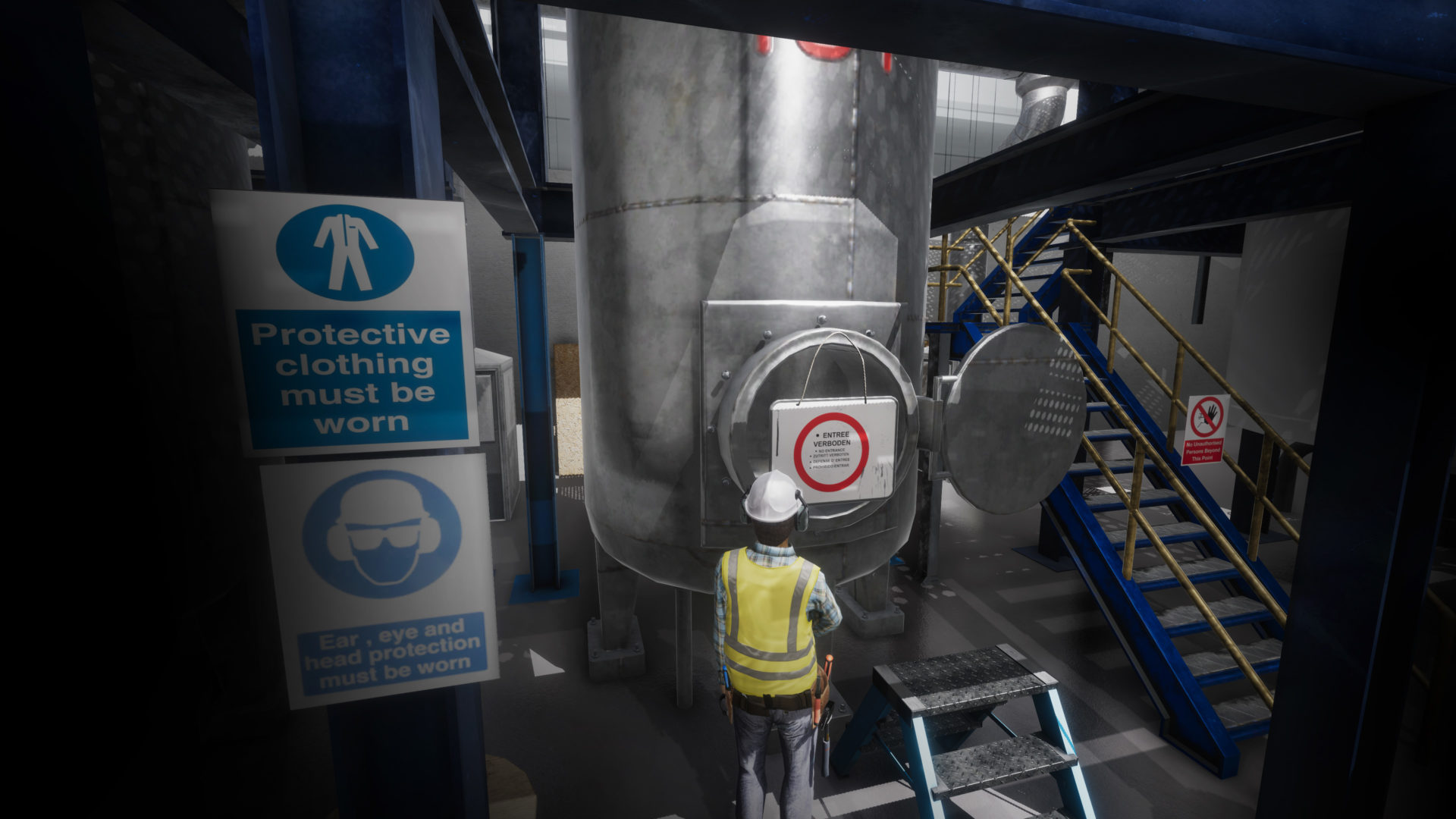
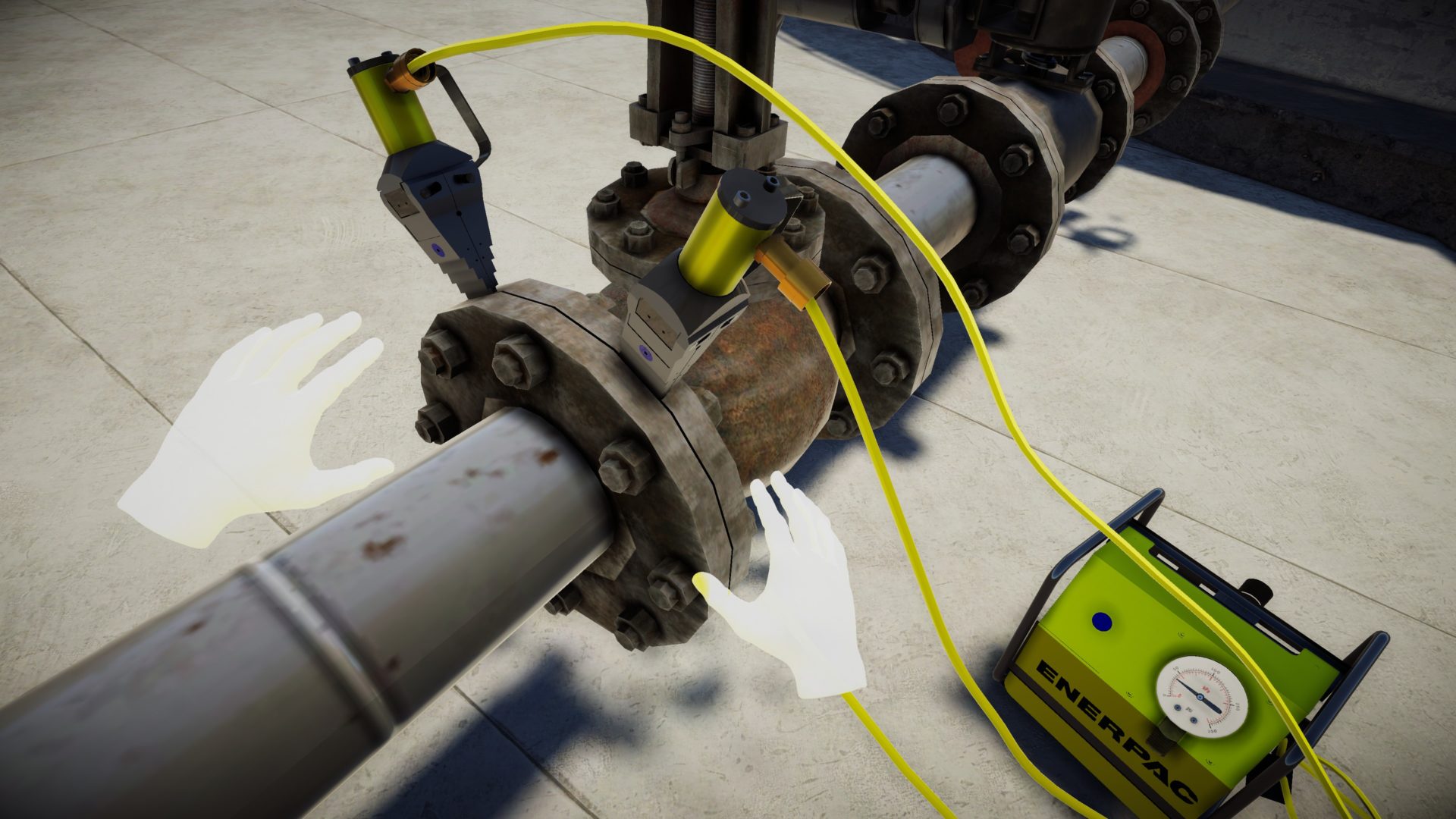
XR training offers a versatile learning tool that transcends the limitations of traditional training methods. By creating realistic and interactive simulations, XR enables trainees to actively engage in experiential learning, leading to increased retention and improved skill acquisition.
The application of XR training is rapidly expanding across various industries, revolutionizing the way we acquire and refine skills. In the food manufacturing industry, XR training enhances employee competence in equipment operation, maintenance, and quality control. XR training in the medical field empowers surgeons with realistic surgical simulations, while medical students can learn vital skills and techniques in a safe and risk-free environment.
Food Manufacturing Industry
The food manufacturing industry demands adherence to strict safety and quality standards. XR training proves invaluable in this context by providing realistic simulations to train employees on various aspects, such as equipment operation, food handling protocols, and hazard recognition. For instance, employees can practice operating complex machinery or simulate scenarios to learn about food safety protocols, ensuring compliance with regulatory guidelines. XR training can also be utilized to simulate emergency situations, enabling workers to develop quick decision-making skills in a safe environment.
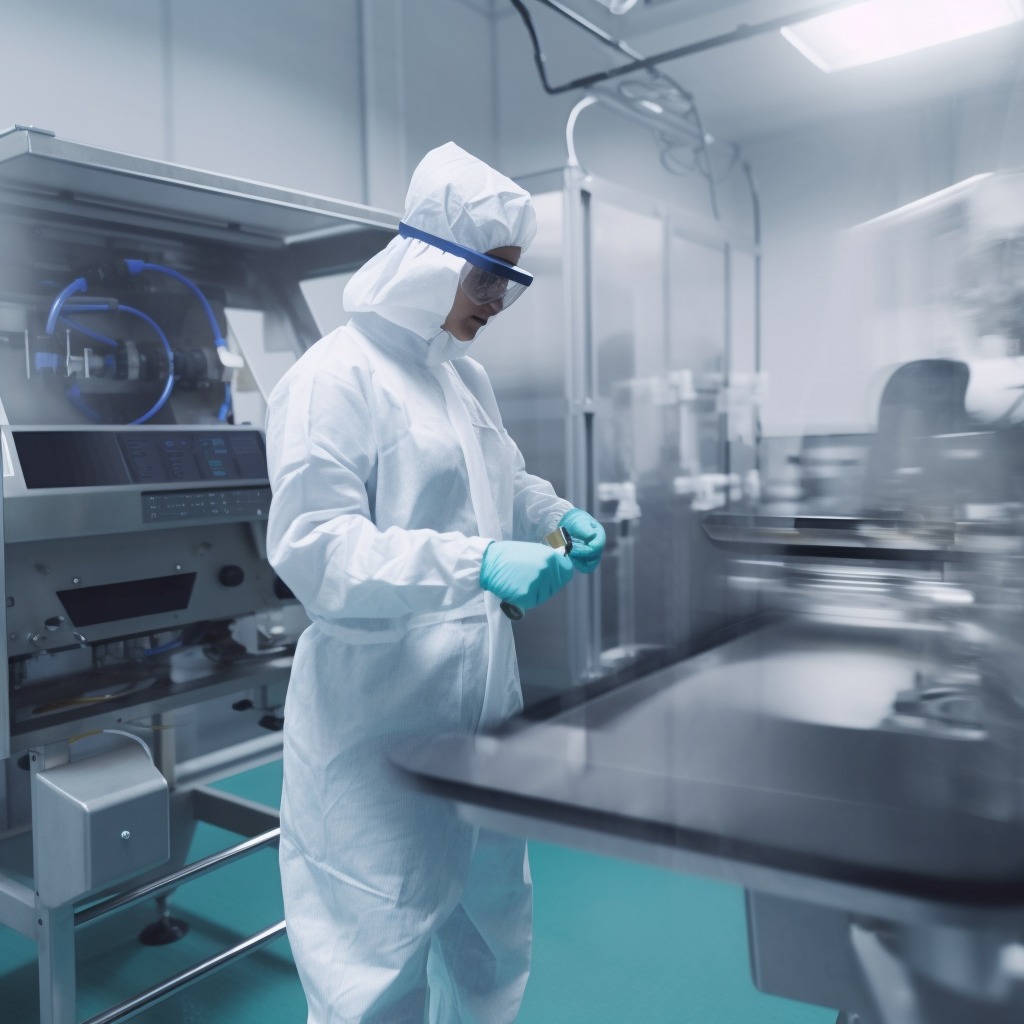
XR Training in the Food Manufacturing Industry
- Equipment Operation and Maintenance: XR training can be leveraged to train employees on the operation and maintenance of intricate food processing machinery. By immersing trainees in a virtual reality training environment, they can practice troubleshooting common issues, learn correct assembly and disassembly procedures, and gain familiarity with the equipment’s control panels. This approach reduces training costs and minimizes the risk of damage to expensive machinery during the learning process.
- Quality Control and Inspections: Ensuring product quality and adhering to regulatory standards are paramount in the food manufacturing industry. XR training can simulate inspection scenarios, enabling employees to identify defects, practice quality control protocols, and learn about specific inspection criteria. This immersive training enhances the accuracy and efficiency of inspections, resulting in improved product quality and reduced waste.
- Food Hygiene: The Luminous team developed an XR application called TraXR aimed at enhancing Food Safety and hygiene processes in food manufacturing. All food factories need to carry out regular audits and swabs for pathogens such as Samella and listeria. Traditionally this is a manual paper-based exercise and open to error. The Luminous app provided hands free operation allowing users to carry out swabs and accurately map the location using the hololens 2 device. The results of swab where then overlaid on to a real-time digital twin of the facility. If a swab did come back positive a user was guided back to the correct location using holographic wayfinding and the cleaning process could then be implemented.
- Market Research: XR can also be used for market research and testing in the Food sector. Luminous created a ground-breaking market research app that allows users to design and build their own holographic rice cakes with hundreds of variations.
- Designing & Visualizing new Equipment: Using devices like the HoloLens 2 holograms of new equipment or machines can be placed in a factory at their correct location at 1:1 scale. This allows engineers to visualise the equipment and check for potential clashes on site.
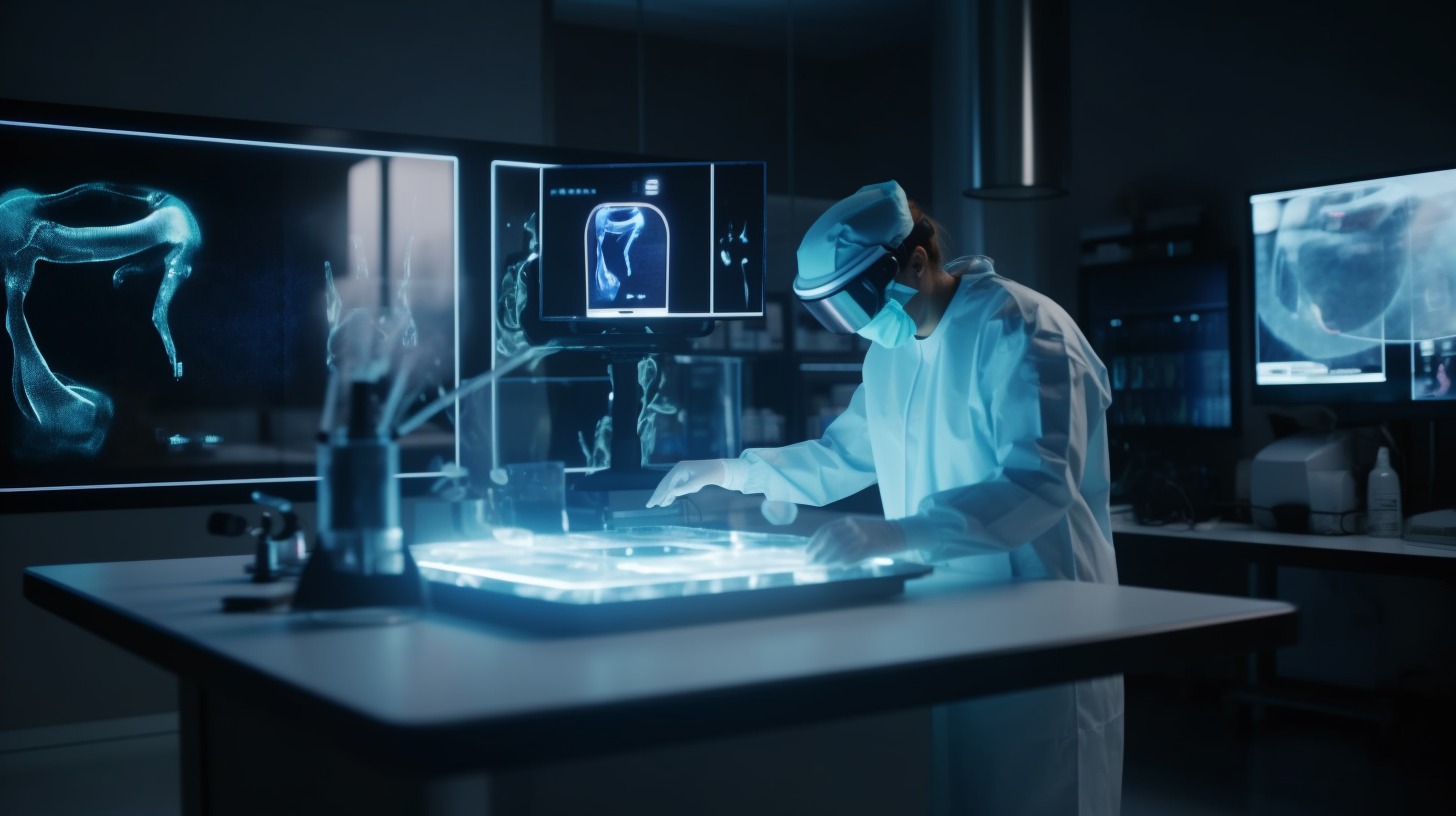
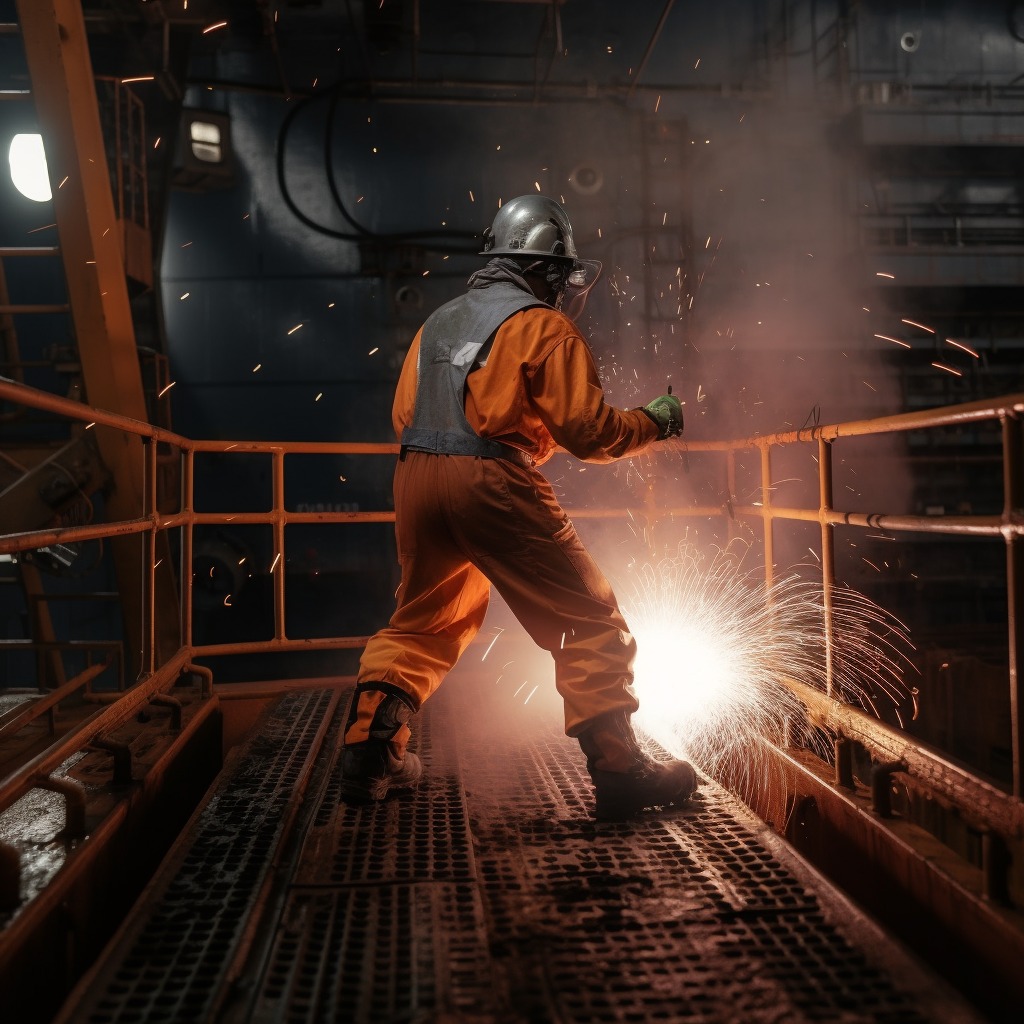
Energy Sector
The energy sector and other hazardous industrial environments can benefit from XR to train staff more efficiently.
Staff working in the oil and gas industry mainly learn on the job, shadowing an experienced operator as many machines operate 24/7 and can’t be switched off. This means it may take months of shadowing before a new operator is allowed to touch the real equipment. XR energy training allows them to train in a safe, controlled environment building up muscle memory and reducing the time competency drastically.
Customers using Luminous upstream outside operator training on tasks such as flushing a level gauge glass have seen student training reduced from 6 months on site to 1 month in XR and then just one month on site. This leads to much faster upskilling of new operators and significant cost savings to the customer.